【导读】基于传感器的过程监控和预测性维护有望实现零停机时间,降低维护成本,改善工人安全性。这些长期利益还没有获得肯定,而之前提供的技术则存在各种限制,或者存在管理成本问题或风险,弊大于利。
与尝试借助一项技术解决复杂问题不同,更谨慎、更具策略性的全系统振动监控视图可实现技术的长期价值。
现在,传感器和传感器处理方面的技术发展可实现完全嵌入式 自主检测系统的部署,并且能够可靠地对设备缺陷、不平衡、 性能变化以及其他异常进行检测和分析,如图1所示。
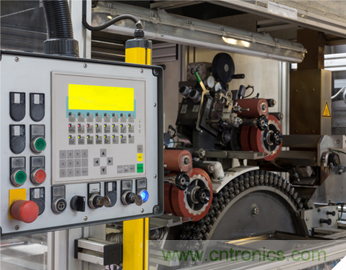
图1. 状态监控和维护的自动化代表无线检测网络的高价值目标
实现完全嵌入式自主检测系统前,必须分析并考虑以下四个主 要系统设计方面:
1. 访问高可信度过程数据
2. 解析和分配数据
3. 考虑过程变化
4. 了解最新技术发展
访问高可信度过程数据
与灵敏电子元件制造业一样,过程监控在高价值设备的生产设 施中可能极其重要。在这种情况下,装配线的细微变化也可能 会导致工厂产量减少,最终设备的主要技术参数变化。过去的 方法是利用手持式振动探头,如图2所示。这种方法的一个主要 缺点是不能进行可重复测量。探头位置或角度稍有改变,就会 产生不一致的振动剖面,从而难以进行精确的时间比较。该方 法的另一个局限性是无法实时指出振动偏移。
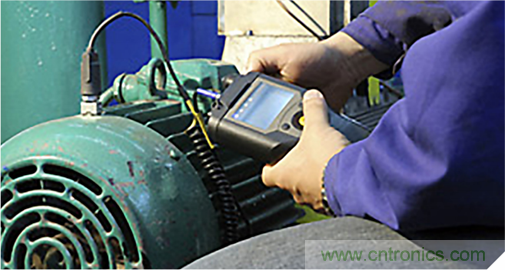
图2. 当前采用的设备变化监控方法缺乏可重复性和可靠性
解析和分配数据
工厂设备通常有多种振动源(轴承缺陷、不平衡和齿轮啮合),其 中包括设计带来的振动源,例如在正常工作过程中产生振动的 钻孔机或压制机。基于时间的分析会产生一个综合所有这些振 动源的复杂波形,如果不进行快速傅里叶变换(FFT)分析,它提 供的信息难以辨别。借助嵌入式FFT功能,自主传感器可实现实 时通知。
许多既有解决方案以压电传感器为基础,其集成度一般非常低,需要依赖FFT外部计算和分析。这不仅使得实时通知毫无可能,而且将大部分额外设计工作推给了设备开发人员。但是,如果传感器内嵌FFT分析功能,就能即时确定振动偏移的具体来源(图3)。从完全集成的传感器开始也可将设备开发人员的开发时间缩短6至12个月。
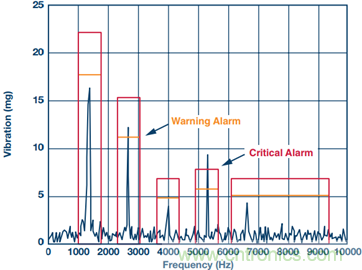
图3. 带可编程滤波和调谐控制功能的嵌入式FFT分析
既有解决方案的另一个问题是大部分都只有模拟输出,这会导致信号在传输过程中衰减,而且离线数据分析非常复杂。可从振动监控受益的大多数工业设备往往存在于高噪声、运动、无法接近、甚至危险的环境中。因此,业界迫切希望降低接口电缆的复杂性,并且在源端执行尽可能多的数据分析工作,以便捕捉到尽可能准确的设备振动状态信息。
集成式、无线(最好)的智能传感器有助于直接使用,并且可在显著降低成本的同时大幅简化传感器网络的部署。但是,部署后仍然存在一些复杂问题,如果不提前处理,就可能会降低系统的完整性。
考虑过程变化
在工厂环境中,振动曲线较复杂、有时间偏移,并且易受设备、材质和位置的变化影响。确定在哪里放置传感器非常重要,其主要决定因素是设备类型、环境和设备的寿命周期。采用高成本传感器元件时,探测点仅限于一个或几个,因此这个问题显得更加重要。更重要的考虑因素是传感器数据本身的完整性。如果没有可靠的传感器,识别出的性能变化可能是由于设备或传感器产生。
基线设备响应是针对设备寿命周期变化调整传感器分析程序时的一个重要工具。利用简单的模拟传感器就能获得基线设备响应,即让操作人员进行测量,执行离线分析,并将此数据与适当的标志一起离线存储在特定设备和探头位置上。更好且更不易出错的方法是将基线FFT存储在传感器头部,这样数据永远不会误放。基线数据还有助于确定报警电平,该值最好也直接在传感器上编程。这样的话,随后的数据分析和采集中,如果检测到警告或故障条件,就可以产生实时中断。
无论是何种技术方法,适用的振动分析程序都应该要能够监控数十甚至数百个位置。在一台设备的整个寿命周期中,可能需要获得成千上万条记录。预见性维护程序的完整性取决于传感器采集点的位置和时间的适当映射。为将风险降至最低,以及获得最有价值的数据,传感器应具有唯一的序列号和嵌入式存储器,并且能够给数据添加时间戳。
即使具有如前所述的良好可追溯性,也存在更具挑战性的问题,即如何以最优方式捕捉到设备性能的细微变化,并使传感器适应各种设备。由于信号和传感器调理和处理取决于具体的设备及其寿命浊气,因此传感器设计过程中存在多个重要考虑因素。
例如,设计人员需要确定,传感器应针对设备故障可能性较小的早期阶段进行配置,还是针对故障可能性较大且更具危害性的晚期阶段进行配置?最好使用可在系统内编程的传感器,以便能够在寿命周期内根据变化调整配置。例如,相对较稀疏的监控(功耗最低)应在早期使用,观察到变化(警告阈值)后,应重新配置为频繁(监控周期由用户设置)监控。
嵌入式模数转换和处理(例如在传感器头部和设备之外)可实现系统内配置和调谐,如图4所示。理想的传感器应提供一个简单的可编程接口,通过快速基线数据采集来简化设备设置、滤波操作、报警编程和不同传感器位置的试验。这种相同的可调谐性与嵌入式基线性能数据结合后,便可在系统内对设备的寿命周期使用嵌入式传感器特性。
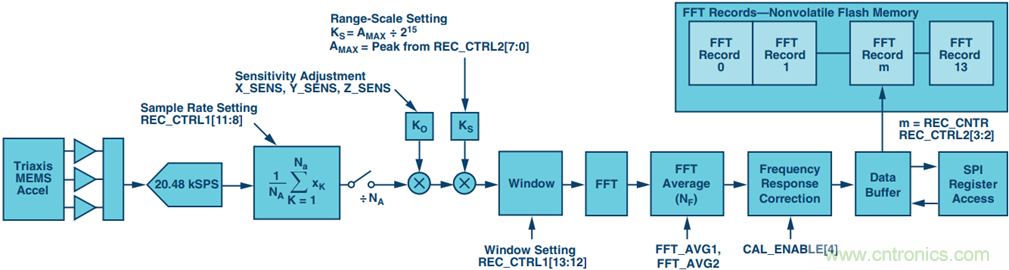
图4. 完全嵌入式智能振动监控系统的典型集成方式
了解最新技术发展
上文重点讨论了现有与过程控制和预见性维护相关的传感器振动监控方法的改善之道。由于容错能力和监控是问题的核心所在,应严格审核传感器本身的可靠性。如果传感器发生故障(性能变化),而不是设备发生故障,该怎么办呢?或者,如果采用完全自治工作的传感器,我们对传感器持续正常工作能有多大信心呢?对于许多传感器,如压电传感器等,这些情况确实会造成严重的限制,因为它们无法提供任何系统内自测。高可信度预见性过程控制程序的基本要求是能够对传感器进行远程自测。这一点现可使用部分MEMS传感器(图5)做到,其中的嵌入式数字自测能够填补可靠振动监控系统的最后空白。
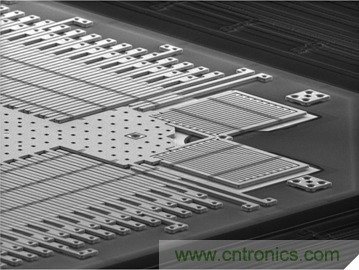
图5. MEMS振动传感器可提供传感器自测的附加优势
通过将MEMS振动检测与无线连接相结合,解决方案现可使多个远程检测接点通过各种无线标准接口与网关节点通信,从而能够整合数据并进行进一步离线趋势分析和学习(图6)。
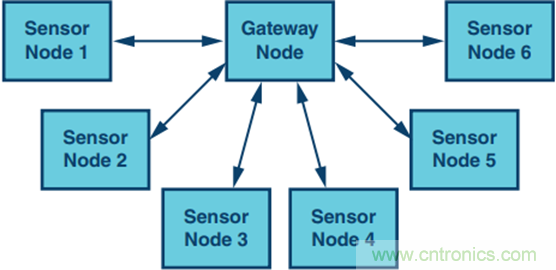
图6. 六个远程传感器接点自主检测、收集、处理数据并无线传送至中央控制器节点
无线连接还可确保振动检测的部署更具普遍性。此类完全集成的传感器无需依赖于翻新接线/基础设施,不仅能够更精确可靠地检测出性能变化,而且能够显著降低预付和重复维护成本。
最后,通过将转换与具有基于云的分析系统的嵌入式连续监控系统耦合,可对当前的设备监控领域中的信息和专门技术产生成倍的影响。借助由MEMS方法实现的更加可靠、功能更强的传感器接点,此传感器到云模型将帮助实现期待已久的实时潜力,以及基于条件的预测性维护。
推荐阅读: