【导读】汽车线束系统是连接蓄电池和各电器元件的主要载体。且在整车零部件中是相对薄弱、易损坏的零件。本文基于整车线束失效解决案例,对线束系统引起的整车失效问题进行系统的归纳总结,并提出基于PDCA有效的改进措施,提高了汽车线束布置与走向设计的稳健性,降低失效频率。
1 引言
线束是汽车的神经网络系统,在整车的运行中传递电压、信号及大量的数据,图1为各用电器线束连接示意图。特别是在互联网、大数据背景下,这就要求线束载体不仅仅起到通断作用,对数据的传输速率及响应能力提出了更高的要求,同时由于线束的物理布置空间有限,对其失效性和售后返修带来更大挑战。
由于汽车安全性、舒适性及环保要求不断提高,汽车上电路数量与用电量显著增加,从而使整车线束成倍增加,在有限汽车空间中如何更有效合理布置已成为汽车制造业面临问题。本文结合汽车生产中产生的线束失效问题进行归纳总结、整理,并提出了有效的改善方案,为汽车线束的设计及布置起到一定指导作用。
线束是汽车的神经网络系统,在整车的运行中传递电压、信号及大量的数据,图1为各用电器线束连接示意图。特别是在互联网、大数据背景下,这就要求线束载体不仅仅起到通断作用,对数据的传输速率及响应能力提出了更高的要求,同时由于线束的物理布置空间有限,对其失效性和售后返修带来更大挑战。
由于汽车安全性、舒适性及环保要求不断提高,汽车上电路数量与用电量显著增加,从而使整车线束成倍增加,在有限汽车空间中如何更有效合理布置已成为汽车制造业面临问题。本文结合汽车生产中产生的线束失效问题进行归纳总结、整理,并提出了有效的改善方案,为汽车线束的设计及布置起到一定指导作用。
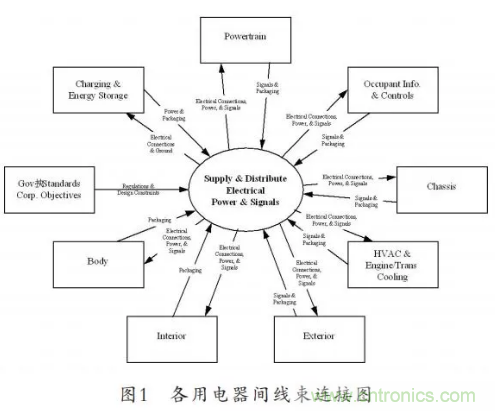
2 汽车线束布置及失效方式
2.1 汽车线束布置方式简介
随着车辆安全、智能、舒适性的发展,传感器、摄像头及ECU占据了一定的空间,从而造成线束的布置空间越发狭小,同时功能的增加意味着导线数量及体积不断增大。整车可装拆性、运输便利性等也对线束提出了更高的要求。下图2 是上汽通用某车型的线束发布图, 为便于运输和装配,将整车线束切割成11个部分。
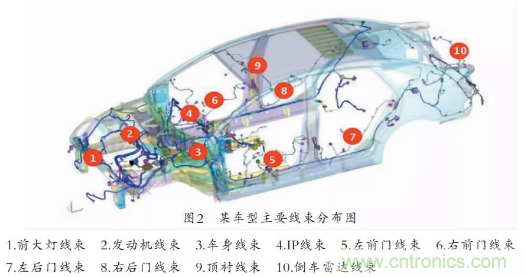
线束是整车中较为薄弱的零件,不论在制造、装配及后续使用中极易破损或失效的。本文从线束的制造、运输及整车的装配和车辆后续的使用等各个环节对线束的失效进行整理,并对典型问题剖析。按失效模式可以分为线束制造失效、整车装配失效、耐久性失效等几大类。
2.2 汽车线束失效方式
2.2.1 线束制造失效
线束主要由导线、端子、接插件、包裹物、卡钉和线槽支架等构成,不规则零部件的构成从而注定了线束制造是一种自动化程度较低、劳动密集型产业。众多的人工操作影响了线束标准化,因此线束制造过程中的失效是一种随机、不可控的失效方式。
如下表1是线束在制造过程中最常见的失效方式,需在制造的各个环节保证线束的制造质 量。机械设备设定合理的规格参数,人工操作建立标准化操作及比对面板,最后对线束进行抽查全方位检测而保证线束的制造质量。
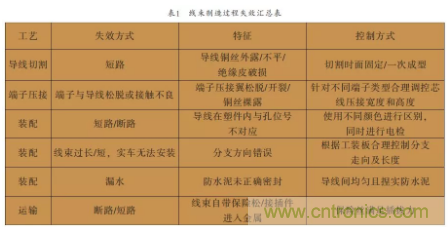
2.2.2 汽车装配失效
线束在实车上的布置依据整车装配工艺会被打散成多个部分,从而提高了可装配型和可维修性。但同时线束接口及定位件的增多意味着失效的概率增加,本部分结合整车在装配环节出现的失效案例进行分类汇总,以提高线束的装配可靠性。
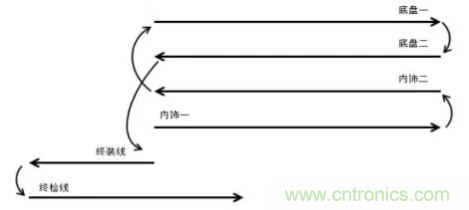
如上图3可以看出线束的装配从总装内饰工位几乎持续到终装工位,跨度非常大,同时接触区域较多。结合其失效方式及表现形式大致分为如下几类:
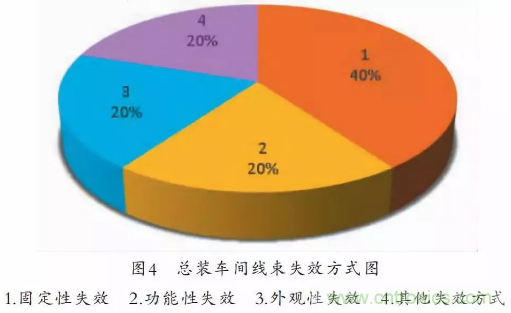
固定性失效为线束本身的定位件在固定孔位或扎带处脱落,此类失效不影响功能,不影响整车使用。
功能性失效是一种比较严重的失效方式,会引起整车某个功能的缺失,严重的将影响到车辆行驶及驾驶者的安全。
外观性失效是一种影响客户感知的失效形式。线束多布置在客户不宜感知的区域,但由于线束供应商工艺或空间等因素会导致附着在其上的零件装配受影响,从而带来匹配或美观问题。
此类问题在前期设计时要考虑线束或接插件运动包络区域是否与周围零部件有干涉风险,从而选择合适的地方布置固定点,保证在满足功能的情况下提高美观性。如下图5为线束在装配过程中被金属锐边磨损失效的典型事例。表2为失效方式及控制方式汇总。
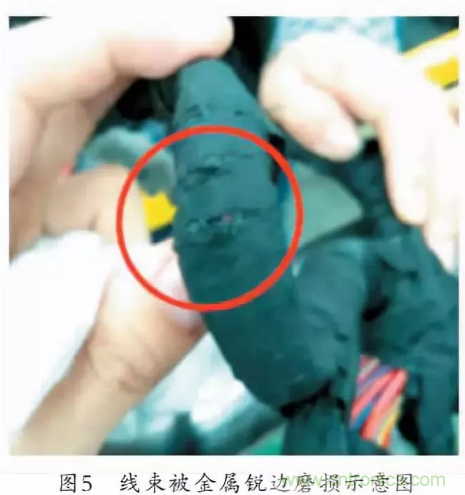
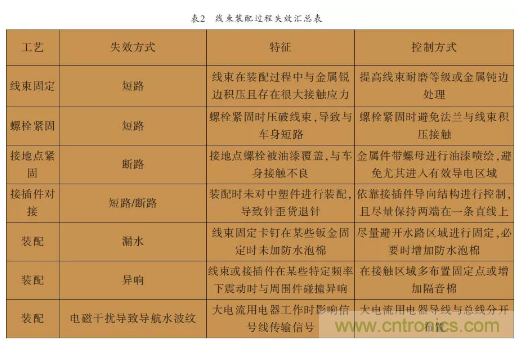
2.2.3 耐久性失效
耐久性失效是一种随着车辆使用,在中间环节形成的失效方式,是伴随着车辆的生命周期随机产生的,具有不可预测性。一旦失效会引起客户对品牌的极大抱怨。此类失效多为线束在运动件包络区域内发生,在达到一定的磨损后产生的,因此在初期不易察觉。如下表3为耐久性失效汇总表。
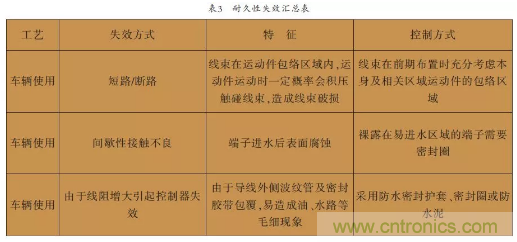
如下为两种典型失效方式,图6为发动机线束与空调补液管之间震动接触造成的磨损,图7为车辆轮速传感器在运动到极限位置时闷头受力后脱落。综上需严格控制线束在运动包络区域的布置,同时针对线束的磨损需遵循严格的评估标准。
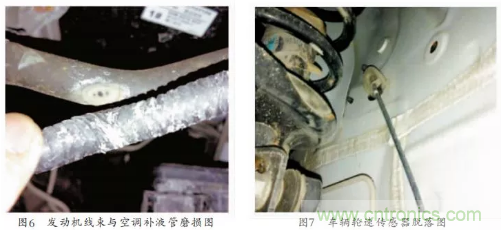
3 线束设计可靠性提高措施
由上可知线束设计是一个不断提高、不断优化的过程,同时应考虑其全生命周期。结合PD- CA的控制方案提出如下图8线束开发设计闭环控制方案。
在整车设计初期,就对线束的布置、运动包络进行充分考虑和识别,同时结合线束零部件的DV/PV实验,不断提高设计薄弱环节,最后在实车装配阶段及售后阶段持续进行关注,并同时把发生的问题进行归类总结,输入到下一个车型的前期开发中,从而避免问题的重复发生,提高虚拟设计和实车表现的一致性。
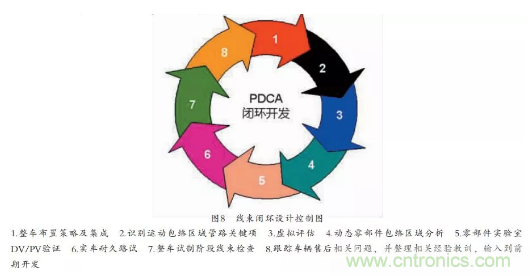
4 结论
线路在整车系统中属于比较容易出现问题的一类零件,只有在前期设计和项目阶段做好充分 的管路评估才能高效的控制线路问题。本文结合通用某车型线束本身制备和整车装配工艺,总结了线束各种失效方式及控制方式,同时提出线束 PDCA的控制方法,为线束在前期设计阶段提供了很好的借鉴。
来源:线束中国