【导读】PBGA是一种封装形式,其主要区别性特征是利用焊球阵列来与基板(如PCB)接触。此特性使得PBGA相对于其他引脚配置不同的封装形式(如单列、双列直插、四列型)有一个优势,那就是能够实现更高的引脚密度。PBGA封装内部的互连通过线焊或倒装芯片技术实现。包含集成电路的PBGA芯片封装在塑封材料中。
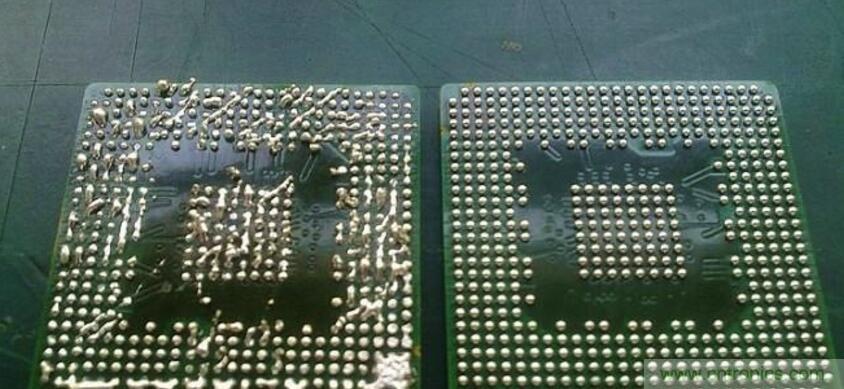
封装描述
PBGA是一种封装形式,其主要区别性特征是利用焊球阵列来与基板(如PCB)接触。此特性使得PBGA相对于其他引脚配置不同的封装形式(如单列、双列直插、四列型)有一个优势,那就是能够实现更高的引脚密度。PBGA封装内部的互连通过线焊或倒装芯片技术实现。包含集成电路的PBGA芯片封装在塑封材料中。
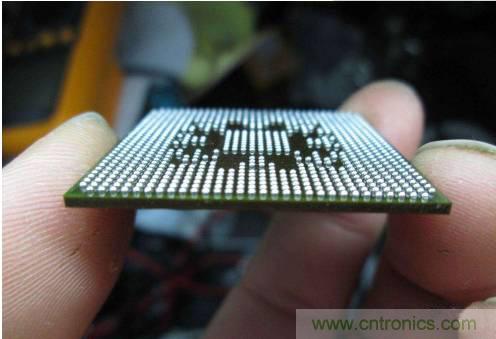
图1. PBGA器件示意图
PBGA器件返修
将PBGA器件装配到PCB上之后,若发现缺陷,应当返修以移除不良器件,并换上工作正常的器件。移除器件之前,应加热不良器件直至焊接接头液化,以便于从电路板上移除不良器件。
常规返修程序如下:
1. 准备板子。
2. 移除器件。
3. 清洁PCB焊盘。
4. 涂敷焊膏。
5. 器件对齐和贴片。
6. 固定器件。
7. 检查。
移除器件和分层
移除器件时,可能会在PBGA和/或PCB上产生机械应力。应小心移除不良器件,避免损伤PCB、邻近器件及不良器件本身,尤其是若用户打算对不良器件进行故障分析时。
PBGA器件上若有过大应力,例如将器件加热到额定峰值温度以上或过度暴露于高温下,可能导致封装分层或外部物理损坏(参见图2和图3)。对于要做进一步分析的器件,移除不当所引起的分层会加大找出真正故障机制的难度。因此,为了进行有效的故障分析,妥善移除不良器件是十分必要的。
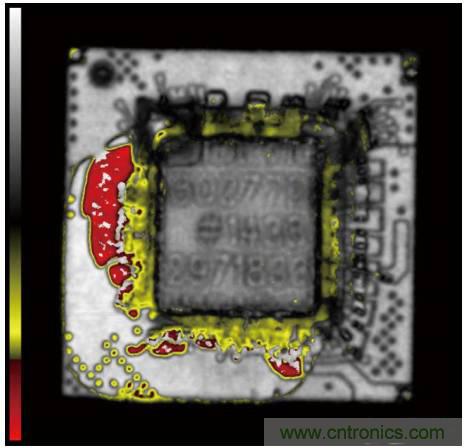
图2. 过度加热引起PBGA器件的基板和塑封材料之间分层(通过扫描声学显微镜观测)
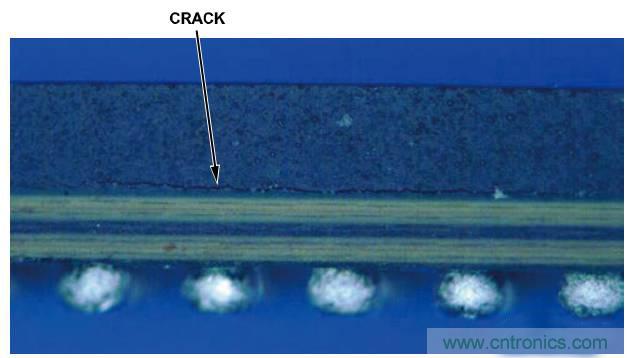
图3. 过度加热导致PBGA上出现裂纹的低放大率图像(侧视图)
准备板子
强烈建议在返修开始前对PCB组件进行干烘,以消除残留水分。若不消除,在回流期间,残留水分可能会因为“爆米花效应”而损伤器件。在125°C下烘烤PCB组件至少4小时,只要这些条件不超过PCB上其他器件的额定限值。如果这些条件超过其他器件的额定限值,则应使用联合行业标准IPC/JEDEC J-STD-033中说明的备选烘烤条件。
移除器件
可使用不同的工具来移除器件。为了移除器件,可能要加热器件,直至焊料回流,然后在焊料仍处于液态时通过机械手段移除器件。可编程热空气返修系统可提供受控温度和时间设置。
返修时应遵循器件装配所用的温度曲线。返修温度不得超过湿度灵敏度等级 (MSL) 标签上规定的峰值温度。加热时间可以缩短(例如针对液化区),只要实现了焊料完全回流即可。焊料回流区处于峰值温度的时间应小于60秒。拾取工具的真空压力应小于0.5 kg/cm2,以防器件在达到完全回流之前顶出,并且避免焊盘浮离。请勿再使用从PCB上移除的器件。
控制返修温度以免损坏PBGA器件和PCB。应当考虑由于热质量不同,相比基于引线框的封装,例如标准外形集成电路 (SOIC) 和引线框芯片级封装 (LFCSP),PBGA的加热速度可能更快。注意,用耐热带盖住器件周围的区域可提供进一步的保护。此外,建议加热PCB下方以降低PCB上下两面的温差,使板弯曲最小。
定义返修工具设置时,应标定温度曲线。首次返修特定器件时,这种标定尤其重要。还需要利用不同的主体尺寸、焊料成分或不同的PCB材料、配置、尺寸和厚度对PBGA器件进行标定,因为它们可能有不同的热质量值。标定必须包括对温度、时间和设备工具的其他设置进行监控(参见图4)。应将热电偶装配到板组件的不同部分,如PBGA器件上部和PCB上部(参见图5)。分析时间和温度曲线数据,从评估中获得器件移除的有效参数。
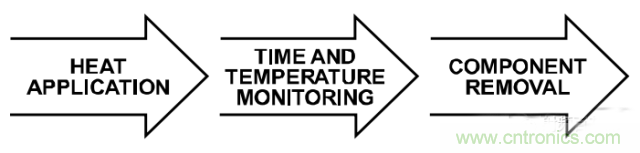
图4. 器件移除评估的简化流程图
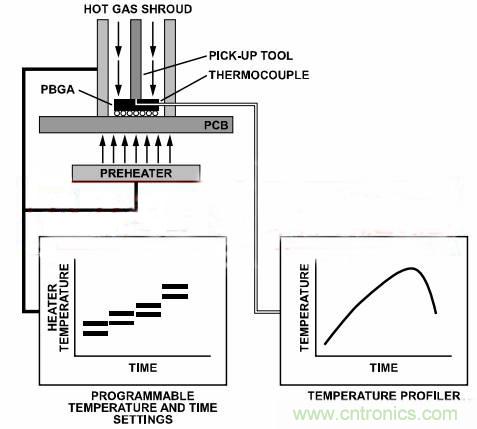
图5. 器件移除标定设置示意图
清洁PCB焊盘
移除PBGA器件之后,PCB上的焊盘会有过多的焊料,必须在安装替换PBGA器件之前予以清理。焊盘清理可分为两步:
去锡。利用吸锡线和刀片型烙铁去除焊盘上过多的焊料(参见图6)。所选刀片的宽度应与器件占用的最大宽度相匹配。刀片温度必须足够低,以避免损坏电路板。可将焊剂涂在焊盘上,然后用吸锡线和烙铁去除过多焊料。
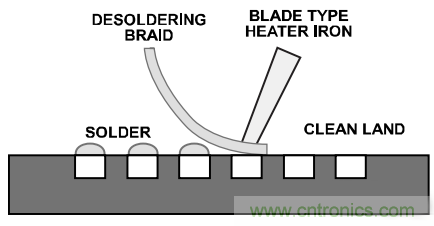
图6. PCB焊盘去锡
清洁。在返修区域上用清洗剂清洁,并用无绒布擦干净。
使用的清洗剂取决于原始总成所用的焊膏类型。
涂敷焊膏
在将替换PBGA器件安装到电路板上之前应涂敷焊膏,目的是取代最初装配电路板时涂敷的焊膏,从而保证PBGA焊接接头的可靠性。给每个焊球涂敷的焊膏量必须一致,以免在电路板上安装PBGA时发生不共面问题。
可利用模板来将焊膏涂敷到PCB焊盘上。模板对齐精度是使回流焊锡处理保持均匀的关键。使用与电路板装配相同的PBGA孔径几何图形和模板厚度。使用梯形孔径(参见图7)以确保焊膏均匀释放并减少污点。
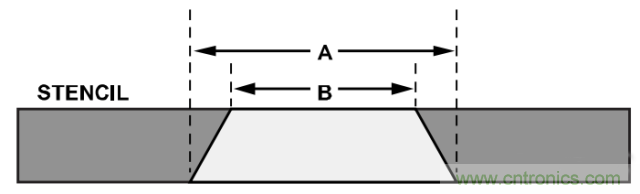
图7. 模板孔径几何图形(A比B长)
某些情况下,利用模板将焊膏均匀精确地涂敷在PCB焊盘上可能不可行,尤其是对于器件密度高或几何空间紧张的电路板。这种情况下,应考虑将焊膏涂敷在器件底部的焊球上。为此,可利用模板将焊膏涂敷在焊球上端,或将焊膏分配给所有焊球(参见图8和图9)。可利用专门设计的夹具和/或返修设备来达到这一目的。
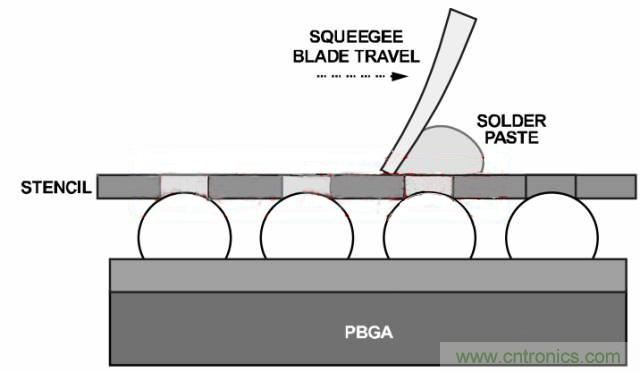
图8. 焊膏模板将焊膏印制到焊球上
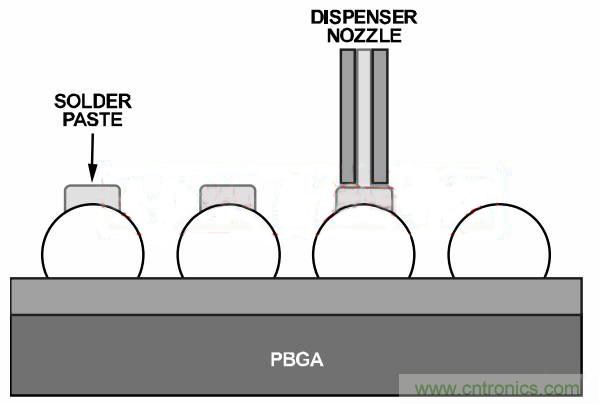
图9. 将焊膏分配到焊球上
器件对齐和贴片
将器件精准贴放到电路板上是很重要的。带分光束光学系统的贴片设备有助于PBGA和电路板的对齐。此类成像系统涉及到将PBGA焊球镜像叠放在PCB焊盘镜像上(参见图10)。贴片机必须具有支持用户沿x轴和y轴进行微调(包括旋转)的能力。
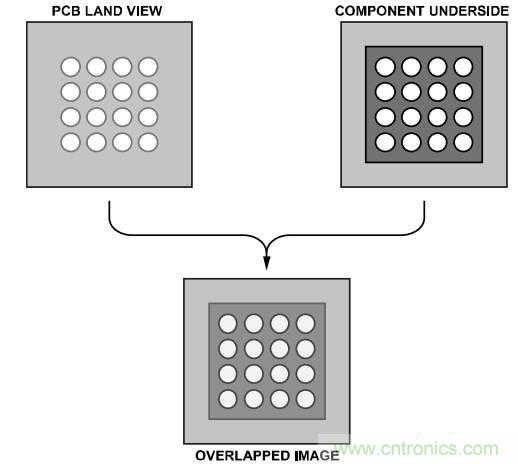
图10. 利用分光束光学系统对齐PCB和器件
贴片精度取决于所用的设备或工艺。虽然PBGA封装在回流焊过程中往往会自动对齐,但应确保贴片偏差小于PCB焊盘宽度的50%。若对齐误差过大,焊料桥接可能引起电气短路。
固定器件
因所有回流参数均经过优化,故应使用原始装配过程中制定的热曲线。
检查
回流之后,检查装配好的PBGA有无缺陷,如未对齐或受损等。利用X射线检查有无问题,如焊料桥接和锡珠等。如有必要,执行电气验证测试以验证器件功能正常。