【导读】智能手机改变了我们的生活,但是人们对智能手机现有的功能仍不满足,希望能用它做更多的事情。同时,在智能手机的基础上又出现了可穿戴设备。但是经过这些年的发展,智能手机和可穿戴设备并没有革新性的技术出现——待机时间仍然只有一天,可穿戴设备的功能依然有限。
三星的手表体积太大,功能有限;谷歌的眼镜虽然创意很好,但它有50g(1两)重,因此它们都没有大卖。谷歌的光学方案是Kindle提供的,虽然他们的方案非常棒,但是它的封装却太大……
可穿戴设备包括眼镜、腕带、手表、鞋和衣服等,手机带在身上,其实也可以算作一种可穿戴设备。日前,在深圳国际电子展ELEXCON 2016暨深圳国际嵌入式系统展EMBEDDED EXPO 2016手机制造分论坛上,深圳凯意科技CEO万滨在介绍“手机3D可折叠封装”时表示,可穿戴设备的共性是体积小、功能多。手机将来会成为一个综合信息终端——它需要植入很多传感器技术,比如PM2.5、气体、心率、血压传感器等等。然而现在很多的传感器还无法做到小型化。另外,灵敏度/准确度也是技术应用的关键因素。作为消费品,这类设备还必须要做到便宜。
举例来说,三星的手表体积太大,功能有限;谷歌的眼镜虽然创意很好,但它有50g(1两)重,因此它们都没有大卖。谷歌的光学方案是Kindle提供的,虽然他们的方案非常棒,但是它的封装却太大。
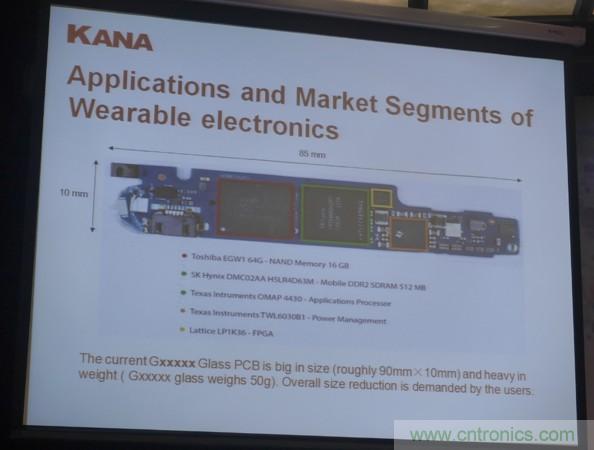
苹果第一代手表S1上用的系统级封装(SiP),是日月光提供的方案,这个封装尺寸为26mm x 28mm,里面集成了大概30多个器件,包括8GB内存和MCU等等。但是这款手表还是未能成功——功能不够;MCU速度慢;过18个小时就要充电(这比手机需要频繁充电还让人难受。手机充电频率最少要做到一个星期,才容易被消费者接受)。
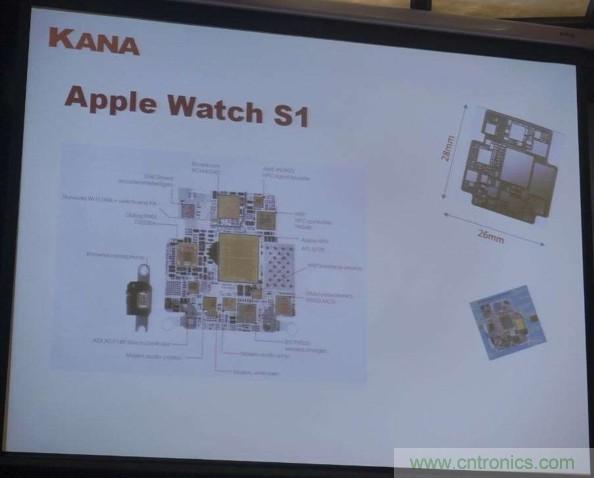
因此,可穿戴设备需要变小、变轻、变得舒适。
“从芯片发展状况看,现在量产的工艺是14nm;TSMC的10nm工艺在2017年将会量产,并且该公司同时在开发7nm工艺。TSMC 7nm估计会在2018年量产,因为其10nm现已拿到高通订单。我相信苹果的下一代处理器也会是10nm。”万总表示
再往下走,机器能达到的极限是7nm。TSMC在这方面明显领先,三星较之晚了半年到一年,7nm可能晚得更多。英特尔10nm的量产计划是2020年。再往下走,半导体的晶格在3到5nm,不可能再小,再小就打破了晶格。这意味着摩尔定律的失效。因此,大家都在想怎么样实现突破。这就出现了3D封装——在空间上发展;在功能上发展,则比如把存储器、MCU和别的功能集成起来,变成一颗芯片,把它们模组化,这就是SiP技术。
但是SiP有很多的表现形式,比如基于晶圆级的,基于不同的基材的,还有将来的TSV通孔技术,即晶圆直接垂直穿孔的技术。在将来iPhone 7、8当中,就会有一颗TSV器件(看不到PCB了)。
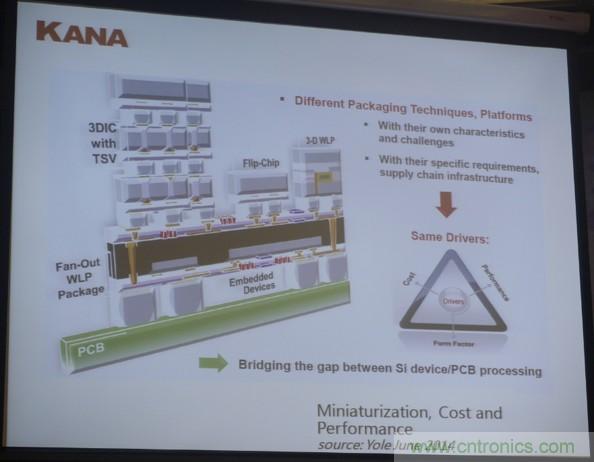
但是对于可穿戴设备来说,像TSV方案和基于晶圆直接组装的SiP方案,整个产业化量产的难度还是很大。另外,它的成本现在暂时还下不来。“因此,在2012年到2013年,我们开展了一个新的设计方法,先把模组的基材由硬基材变成软基材,然后在这个软基材上直接贴上晶圆。软基材相对硬基材可折叠,然后把软基材折叠起来(S型或U型折叠),这样就变成了一个小小的模组,然后再把这个小小的模组封胶起来,就变成一个器件。然后再用这个模组来做手表方案。”万总透露。
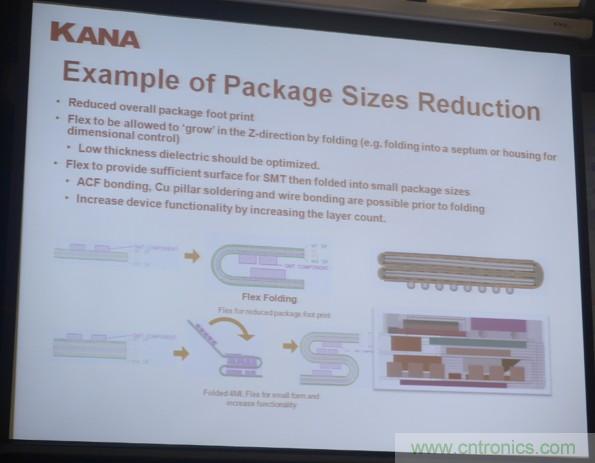
要实现这个方案,首先是要实现这样的基材。现在基材能达到的水平是,基材最终是要封胶的,不会受到外力影响,所以中间很多的加强层和结构层我们可以去除掉。“这样基材就可以做得很薄,当时是0.18mm,现在经过实验,我们完全有能力双面基材达到0.1mm的水平,而且最高可以做到6到8层。”万总说。基材变薄,它的性能也能得到改善——基材弯折会有回弹,在多次回弹之后,基材在多次受热封胶后很容易断裂;将基材变薄后它回弹的应力就会很小,这就提高了可靠性。
装配的难点在于,一是基材要平整——它是软的基材;二是采用什么样的晶圆封装技术;三是整个器件的热设计;四是要考虑可折叠性。然后在工具/设备方面,它的精度要提高;它需要很大产能——成本才能做低;它的可操作性要好。
“我们在2013年决定采用铜柱技术。在裸晶圆上长出凸点的时候,如果是锡球,它的凸点间距没办法做到太小——做到120μm以内就比较困难了。这样会导致整个芯片的功能/计算速度不够。因此,我们后来改成了铜柱工艺,即先在晶圆上长铜柱,在铜柱上再做铜帽,这样凸点间距就可以去到40、30μm,理论上可以去到20μm。实际上,我们用的是80μm,并将多个单元封装在一个软板上。”万总表示,“我们当时觉得铜柱工艺是一个比较好的选择,现在这也被整个产业证实了——70-80%高精密度的用在SiP方面的裸晶圆贴装,现在基本上都是这个方向。”
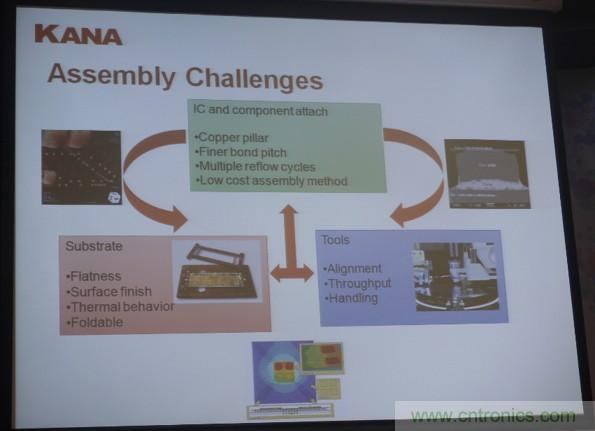
另外,铜柱技术采用的贴装技术也和以前的不同——它是直接进行晶圆贴装。晶圆在减薄到120μm时,贴装很容易破碎,经过测试,压力在0.5N时可以实现快速贴装。
下图是凯意公司最后实现的可穿戴设备产品方案。经过折叠后,芯片封装尺寸减小到6mm x 4mm x 2.6mm,其中包括了MCU、蓝牙、触控、手势控制、加速度计和陀螺仪以及时钟、心率等。
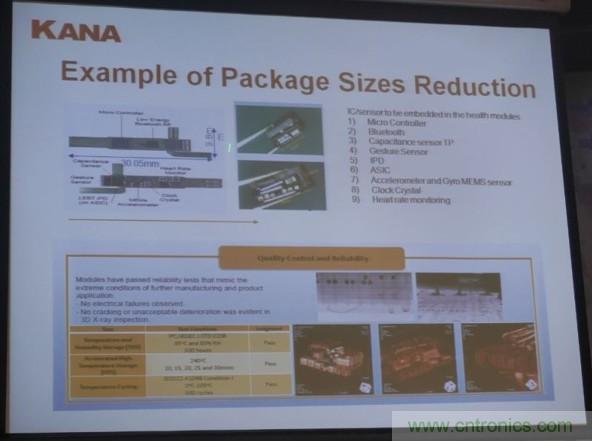
在未来的可穿戴设备里,这种芯片方案具有以下优点。一是成本低。虽然机器变贵、无尘车间级别变高,但是它使用裸晶圆来贴装,省去了封装的成本(封装成本占整个晶圆的30%),而且出货时间更快。二是体积小。三是功能多——苹果手表上采用的是硬板,不可能有可折叠软板这么多的功能。四是更可靠,因为最后要封胶,万总总结说。
推荐阅读: