【导读】现如今的电动机位置传感方式多种多样,光学编码器因其高精确度和易受微控制器控制的标准化“ABI”输出而倍受电机控制系统设计者的青睐。
现如今的电动机位置传感方式多种多样,光学编码器因其高精确度和易受微控制器控制的标准化“ABI”输出而倍受电机控制系统设计者的青睐。
但由于多种原因,非接触式磁性位置传感器现在成为了更好的选择。由于磁性位置传感器的尺寸更小,能够抵御灰尘、油脂、水汽等污染物,因而能够作用于对尺寸和/或可靠性有更高要求的应用。
在过去,有一个对磁性位置传感器不利的趋势:新型无刷直流(BLDC)电动机在总体上有高效率目标,以减少功耗。与此同时,设计者被赋予了增加新电机力矩的任务,实现电机的低转速运行,以支持直接驱动系统。最终,变速器将不再是必需品,这就大大降低了物料成本。
要使得力矩和效率达到最大化,无刷直流电动机在高转速下就必须有一个极其精确的发动机旋转角度数据——利用传统的磁性传感器是很难得到的。现在,新一代产品已经实现了传感器设计的一大突破,它们能够几乎完全精确地测量高转速下的旋转角度。
如何实现角度测量
一个无刷直流电动机包含了一个永磁电动机(转子)和三个或三个以上等距的固定线圈(定子)。通过控制固定线圈中的电流能够形成一个任意方向和大小的磁场。力矩来源于转轴上运行的转子和固定线圈之间的引力和斥力。
当固定线圈磁场与转子磁场相互垂直时,力矩达到最大值。所测量的转子角度反馈到通过固定线圈控制电流的系统(见图1),产生一个垂直磁场。
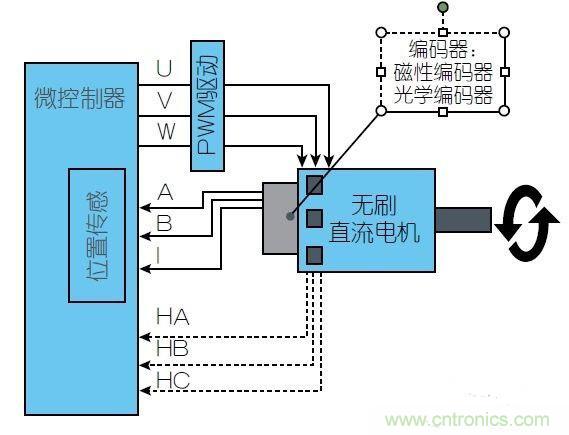
图1:一个无刷直流电机控制系统需要通过磁性位置传感器(通常用于汽车领域)或光学位置
在多数高端应用中,无刷直流电动机正在被永磁同步电动机(PMSM)所取代。永磁同步电动机代替了无刷直流电动机中受转矩脉动影响的模块换相方案,而且能在线圈之间自如切换,减少振动,获得更高的效率。
当然,尽管工业和汽车电动机设计的效率和可靠性必须经常得到优化,许多其他电动机,尤其是消费产品领域的电动机还是最注重成本。对于简单的电动机来说,霍尔开关阵列提供了合适的位置测量方法,也能产生适当的力矩,使操作变得流畅。
但是霍尔开关阵列的精确度和准确度常常达不到高性能发动机对力矩和利用率的要求。相反地,磁性编码器(将霍尔传感器集成到硅芯片中的一个半导体)能够产生高精确度、高分辨率的位置数据。它能够对静止状态或低转速下的转轴进行精确的测量。与工业应用常用的光学编码器不同,磁性位置传感器不会受到污染物的影响,且占用空间很小。
另一方面,大多数霍尔传感器芯片有两大缺陷:传输延迟导致的高转速下动态角度误差;在杂散磁场环境下需要屏蔽措施。
这些缺陷会增加系统成本,削弱系统性能。动态角度误差补偿需要很强的处理能力,对杂散磁场中的IC进行额外的保护也会增加硬件的物料成本。
动态角度误差的起因
霍尔传感器芯片连续地抽样读取转轴上磁铁的磁场强度。芯片被安装在一个固定位置,其表面平行于旋转磁铁的表面,芯片和磁铁之间通常有1到2毫米的空隙。
芯片中包含一个信号调节与处理回路,将测量出的磁场强度换算为转子的角度位置(以度数形式)。这一转换所需的时间就是芯片固定的传输延迟(见图2)。不同芯片延迟持续的时间不等,但当今市场上的芯片传输延迟通常在10μs到400μs之间。
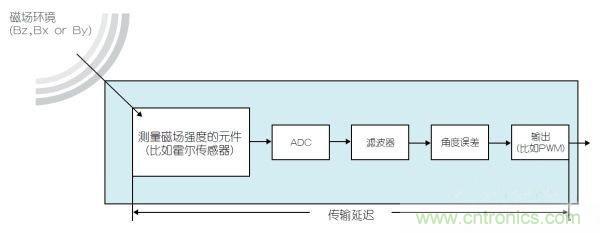
图2:磁性位置传感器中的信号处理导致传输延迟
传输延迟的问题在转子转动时导致了动态角度误差。动态角度误差会随着速度呈线性增长;传输延迟和速度越高,动态角度误差就越大。(见图3)。
图3显示了动态角度误差的增加。假设芯片在转子处于红线位置时读取磁场强度,且芯片在转子转动时的传输延迟为100μs。当芯片将磁场强度换算为角度时,转子用100?s的时间转到了蓝线位置——但芯片向ECU或MCU显示转子仍在红线位置。
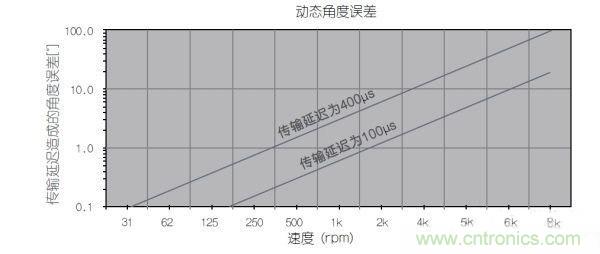
图3:动态角度误差和转速之间的线性关系
在没有误差补偿的情况下,调整方案中的电流会到红线位置的启动线圈中去,而不是蓝色位置,结果导致系统无法将力矩最大化,从而浪费能量,降低系统效率。
如果芯片的传输延迟是100μs,发动机的转速为1000转每秒,那么动态角度误差为1.2度。如果转子的转速增至10,000转每秒,动态角度误差就增至12度。
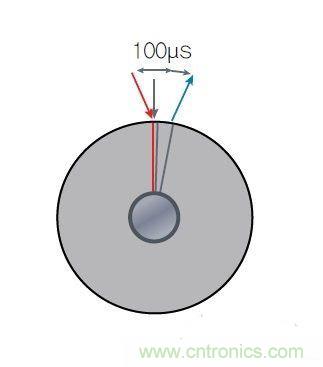
图4:传输延迟如何增加动态角度误差
传输延迟是所有磁性位置传感器的特点,因此系统设计工程师试图将补偿算法应用于减少动态角度误差。不幸的是,每秒几千个数据样本的补偿会对主机ECU造成严重的负担,甚至需要额外定制一个误差补偿专用的MCU。
设计团队并不希望从本质上增加物料成本,也不想花费太多时间来开发、测试和修正他们的补偿算法。
新型传感器减少动态角度误差
如刚才所说,磁性位置传感器的传输延迟是固定的,而动态角度误差的值取决于传输延迟的时间和转速。
现在,奥地利微电子已经开发出新的补偿方案应用到磁性传感器中,该方案正在申请专利。这种新的内部补偿技术叫做DAEC(动态角度误差补偿),首先试用于47系列的磁性传感器。DAEC能够有效减少汽车位置传感器AS5147的传输延迟误差至仅1.9μs。这意味着AS5147在14,500转每秒的转速下,动态角度误差仅为0.17度,几乎可以忽略不计。
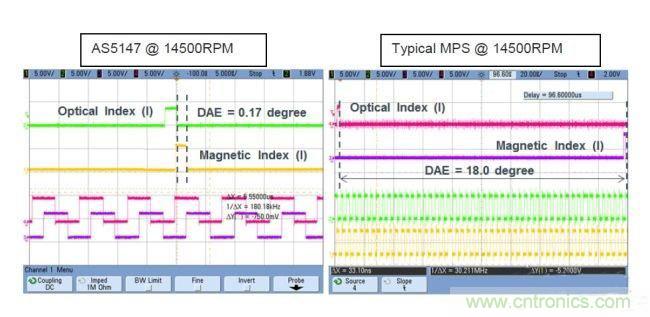
图5:集成补偿方案的传感器输出(左)以及未集成补偿方案的传感器输出(右)
图6显示了AS5147(左)与传统磁性位置传感器(右)测量输出的区别,有精确的光学编码器输出作为参考。右图显示传感器输出受到200μs传输延迟的影响,在14,500转每秒的转速下产生的动态角度误差为18度。
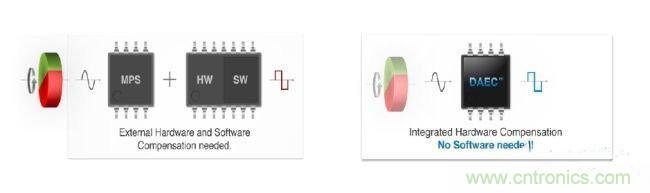
图6:左图显示了传统的分散式动态角度误差补偿法。右图显示了新的动态角度误差补偿法。
相反,AS5147的误差几乎可以忽略不计,也就是说它的信号能够直接用于调整控制器,无需外部补偿。事实上,带有DAEC技术的内部补偿产生的动态角度误差可能比外部补偿更小,因为ECU和MCU中常常会有抽样误差。
当然,传感器内部补偿还能降低系统成本,原因是没有额外的MCU,又或是能够使用更小功率的ECU。
抵御杂散磁场
许多磁性传感器的另一个弊端是容易受到杂散磁场的干扰。转子磁铁以外的磁场干扰随时会破坏芯片的角度测量,而这种随机的错误无法通过主机ECU或MCU来补救。因此,用户不得不对芯片采取屏蔽措施,这就增加了物料成本和装配成本;还可能违背对空间有要求应用的结构设计。
根据ISO 26262汽车功能安全标准,免受杂散磁场的干扰已经成为发动机系统的强制性要求。
“差分传感”专利技术被应用于奥地利微电子的所有磁性位置传感器中,包括47系列,使传感器免受杂散磁场影响的最高值达到25,000A/m。低于该临界值,就无需采取屏蔽措施。
结论
奥地利微电子DAEC技术的推出意味着无刷直流电动机和永磁同步电动机制造商能够利用极其精确的位置数据使高转速应用中的转矩达到最大化,同时通过磁性位置传感器缩小电动机的尺寸,提高可靠性。
DAEC技术现已应用于AS5147*单层晶圆)和AS5247(双层冗余晶圆)汽车磁性位置传感器(AEC-Q100 阶段0汽车应用认证),支持无刷直流电动机在汽车领域的应用,如电子动力方向盘(EPS)、传动装置(变速箱、促动器)、泵以及制动器。
在工业应用方面,采用DAEC技术的AS5047D也已投入使用,提供十进制ABI输出,是替换光学编码器的理想之选。
盘点德州仪器元器件在智能建筑上的应用
崴敏自动化带您饱览“切割”工艺
汇光科技邀您透视光学的艺术
深度解析陀螺仪传感器工作原理
简述纯电感电路中电压与电流的关系